Exploring Top Alternatives to the Best Filling Machine for Efficient Production
As industries continue to evolve, the demand for efficient production processes has led to significant advancements in technology, particularly in the realm of filling machinery. The filling machine, a cornerstone in various sectors including food and beverage, pharmaceuticals, and cosmetics, plays a crucial role in ensuring that products are packaged accurately and swiftly. However, with the rapid development of technology and innovations on the horizon for 2025, it’s essential to explore top alternatives that could enhance productivity and address specific operational challenges. This blog delves into the best alternatives to traditional filling machines, highlighting their benefits and features that can empower businesses to streamline their production lines and maintain a competitive edge in an ever-changing market landscape.
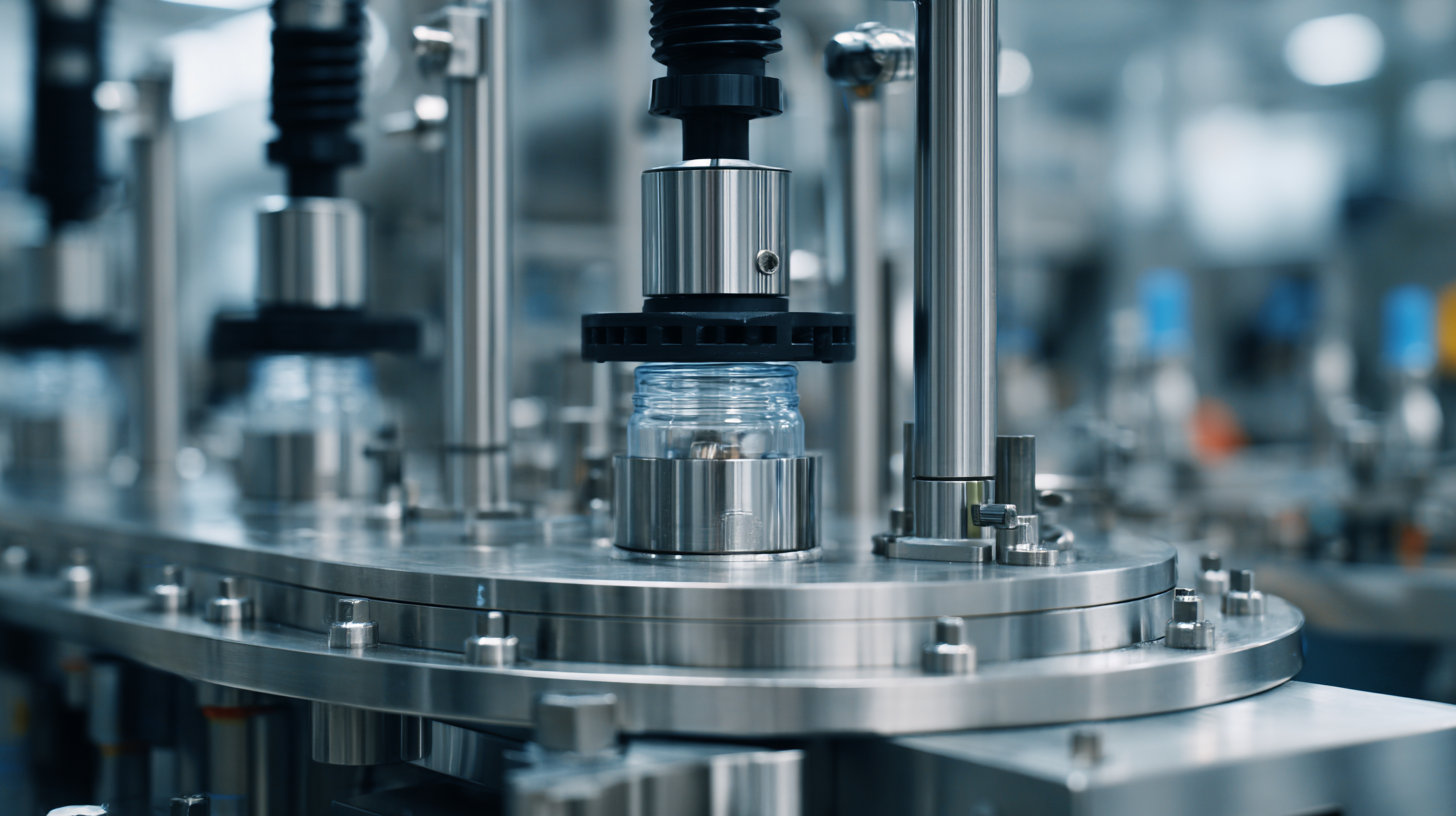
Characteristics of Various Filling Machines for Different Products
When it comes to selecting the right filling machine, understanding the characteristics of various models is crucial for ensuring efficient production. Each machine is designed with specific products in mind, catering to different viscosity levels, bottle shapes, and production speeds. For instance, liquid filling machines often utilize gravity or piston filling methods, which are ideal for thin liquids like water and juices. In contrast, thicker products such as creams or sauces might require a vacuum or gear pump system, ensuring precise filling while maintaining the integrity of the product.
Moreover, the choice of filling machine can also depends heavily on the packaging type. For example, automatic filling machines are designed for high-volume operations using rigid containers, while semi-automatic machines are typically better suited for smaller batches or specialized products. Additionally, some systems come equipped with advanced features like PLC controls or touchscreen interfaces, enhancing ease of use and reducing the likelihood of errors. By carefully evaluating the nuances of each filling machine, manufacturers can significantly improve production efficiency and product quality, making informed decisions that align with their specific operational needs.
Exploring Top Alternatives to the Best Filling Machine
This chart illustrates the efficiency of various filling machine alternatives for different products based on production speed (containers per minute). It provides insights into the performance characteristics that make each machine suitable for specific applications.
Key Features to Consider When Choosing a Filling Machine
When selecting a filling machine, it is crucial to consider several key features that directly impact production efficiency and overall performance. As the global liquid filling machines market is projected to grow from $6.82 billion in 2025 to $10.39 billion by 2032, with a CAGR of 6.2%, the demand for efficient and reliable filling solutions is clear. Understanding the specific needs of your production line, such as the type of liquid being filled and the required speed, can help narrow down your options.
One essential feature to look for in a filling machine is its compatibility with various bottle sizes and shapes. A versatile machine can adapt to changes in product lines without significant downtime. Additionally, consider the accuracy and precision of the filling process; machines that boast high fill accuracy can reduce product waste and improve overall operational efficiency.
Tips: Always check user reviews and case studies related to specific filling machines, as real-world applications provide valuable insights into performance. Moreover, benchmarking different machines against your production requirements will ensure that you choose the best alternative for your specific needs.
Top Alternative Filling Machines for Specific Product Types
When exploring filling machines, it’s crucial to recognize that different products require
specialized solutions for optimal efficiency.
For instance, liquid products like lotions or oils benefit
from piston filling machines, which allow for precise measurement,
minimizing waste and ensuring consistency.
Alternatively, for thicker products such as pastes or gels, a rotary filling machine can
provide the necessary speed and precision, enhancing productivity in a fast-paced production environment.
Moreover, powder-based products necessitate unique filling machinery designed to handle the flow characteristics of powders. Selecting a vibratory or auger filler can facilitate accurate portioning and help prevent product clumping. By focusing on the specific requirements of each product type, manufacturers can choose the most appropriate filling machine alternatives that not only improve production efficacy but also maintain product quality and safety. Understanding these nuances ensures that every type of product is filled correctly, addressing various market needs effectively.
How to Optimize Production Efficiency with the Right Filling Equipment
In today’s fast-paced manufacturing environment, optimizing production efficiency is paramount for companies aiming to stay competitive. In the food and beverage industry, for instance, efficient steam energy production has been recognized as a crucial factor for reducing operational costs and enhancing productivity. It is reported that improved steam energy processes can lead to a significant reduction in energy consumption—potentially cutting costs by up to 30% while maintaining high output levels.
Moreover, advancements in technology, such as AI-driven tools and robotic solutions, are redefining production methodologies. For example, new robotic gap filling machines have been implemented to ensure that plant trays are filled to perfection, mitigating inefficiencies caused by missing plants during transplantation. This innovation not only optimizes labor but also improves yield, highlighting the importance of integrating cutting-edge equipment into the production line. Furthermore, as sustainability becomes a key focus in manufacturing, optimizing equipment for eco-friendliness can lead to long-term savings and reduced environmental impact, underscoring the need for manufacturers to rethink their strategies for production efficiency.
As the industry evolves, the utilization of machine vision technologies and AI for quality control is revolutionizing the approach to manufacturing processes. These advancements allow manufacturers to maintain high standards while boosting speed and reducing waste, reshaping the future of production efficiency across various sectors.
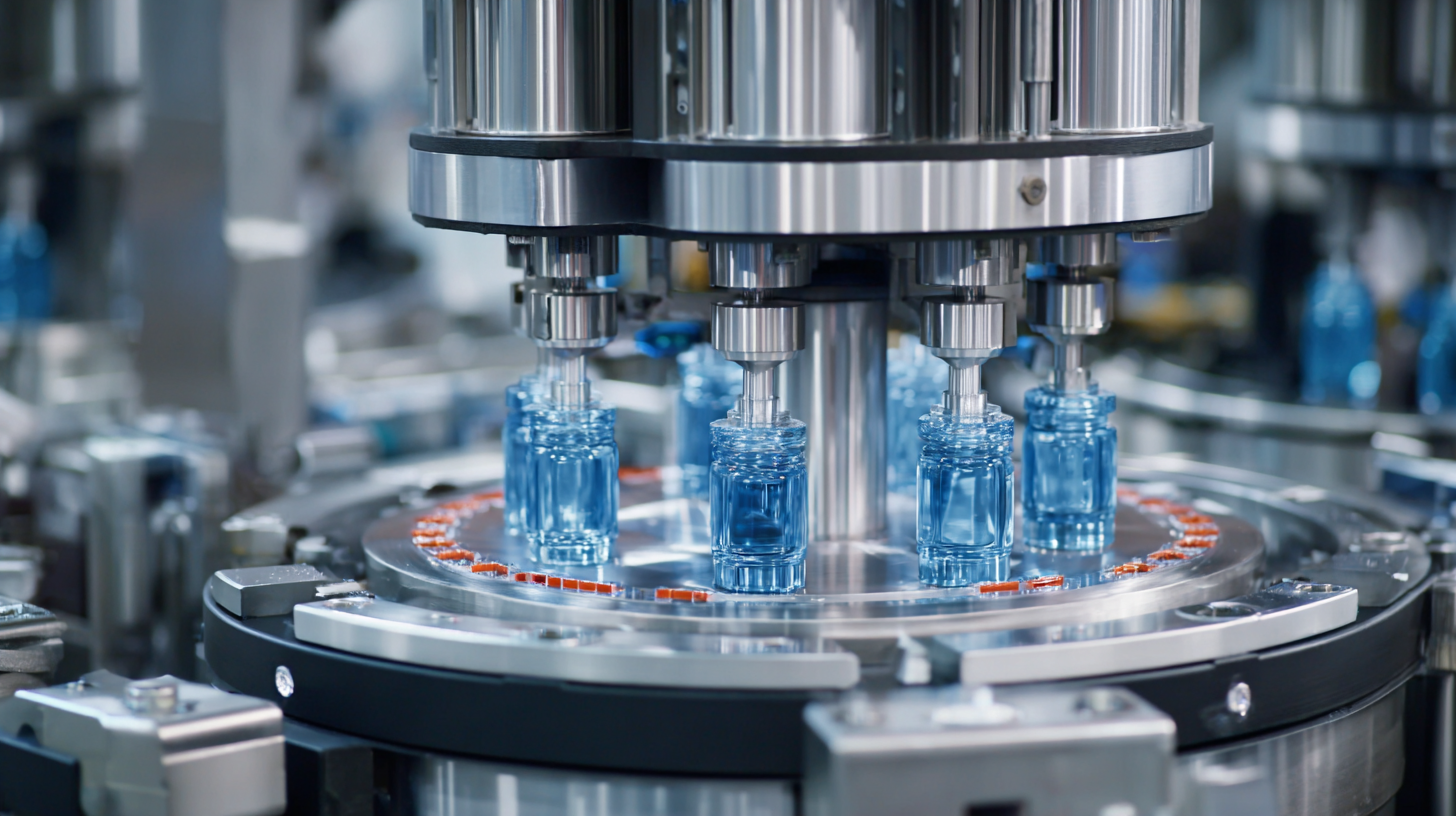
Comparative Analysis: Pros and Cons of Common Filling Machine Types
When it comes to selecting a filling machine, manufacturers often face the dilemma of which type best suits their production needs. Common filling machine types include volumetric, gravimetric, and piston fillers, each presenting distinct advantages and disadvantages. Volumetric fillers are known for their speed and efficiency in handling liquids, making them a popular choice for high-throughput operations. However, their precision can be compromised when dealing with varying viscosity levels, leading to inconsistent fill weights.
On the other hand, gravimetric fillers excel in accuracy, as they measure the weight of the product before dispensing. This type is particularly advantageous for industries requiring high precision, such as pharmaceuticals and chemicals. Nonetheless, the complexity of these machines often translates to higher maintenance costs. Piston fillers offer versatility and are excellent for products with large particulates or thicker consistencies. Their ability to handle a diverse range of products is a significant pro, but they generally operate at slower speeds compared to other types, potentially becoming a bottleneck in high-speed production lines. Understanding these pros and cons is crucial for manufacturers aiming to optimize their filling processes.
Exploring Top Alternatives to the Best Filling Machine for Efficient Production - Comparative Analysis: Pros and Cons of Common Filling Machine Types
Filling Machine Type | Pros | Cons | Ideal For |
---|---|---|---|
Gravity Filling Machine | Simple operation; low cost; suitable for thin liquids. | Not suitable for thick products; slower filling speed. | Small-scale production of non-viscous liquids. |
Piston Filling Machine | Highly accurate; can fill viscous products. | More expensive; requires maintenance. | Medium to large-scale operations, especially with thick liquids. |
Volumetric Filling Machine | Fast and efficient; consistent volume control. | Can be complex to operate; higher upfront cost. | High-speed production environments. |
Ampoule Filling Machine | Ideal for sterile applications; accurate dosing. | High maintenance; requires skilled operators. | Pharmaceutical and laboratory settings. |
Tabletop Filling Machine | Compact; easy to use; budget-friendly. | Limited production capacity; manual operation. | Small businesses and startups with low volume needs. |