Ultimate Guide to Choosing the Best Filling Machine for Your Business
In the fast-paced world of manufacturing and packaging, selecting the right filling machine is crucial for operational efficiency and product quality. According to a recent report from MarketsandMarkets, the global filling machine market is projected to reach $7.8 billion by 2026, growing at a CAGR of 5.8% from 2021. As businesses aim to enhance productivity and reduce costs, the importance of investing in the most suitable filling solution cannot be overstated. With various types of filling machines available, tailored to different products and production scales, companies face the challenge of making informed choices. This ultimate guide will delve into the top strategies for selecting the best filling machine that aligns with your specific business needs, ensuring you leverage the right technology to stay competitive in the industry.
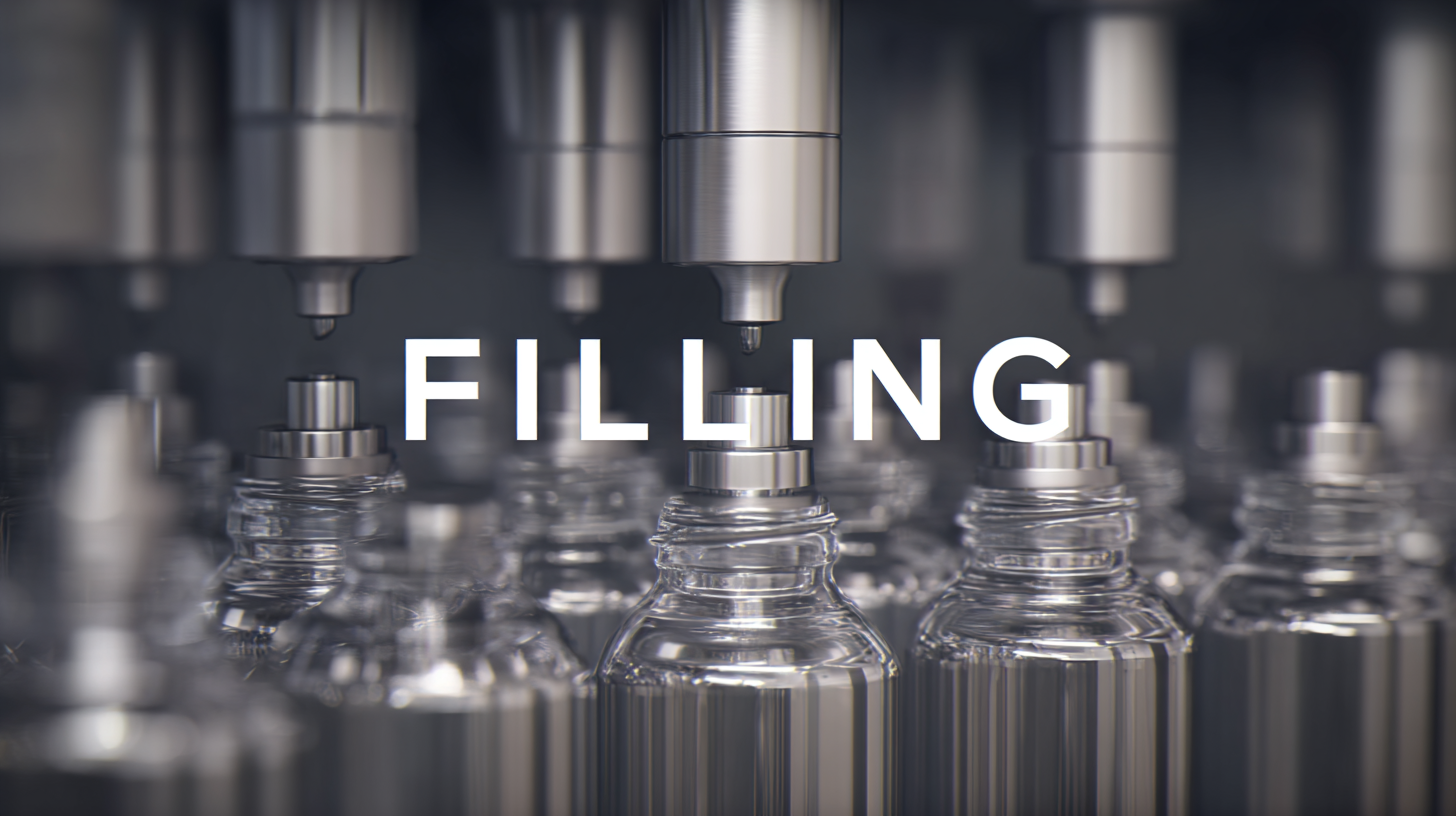
Understanding After-Sales Service Benefits for Filling Machines
When investing in a filling machine for your business, understanding the benefits of after-sales service is crucial. A reliable after-sales service can greatly enhance operational efficiency and minimize downtime. Manufacturers that offer comprehensive support often provide timely maintenance, troubleshooting, and spare parts supply, ensuring that your machine runs smoothly for years. This level of commitment not only protects your initial investment but also enhances productivity, allowing you to focus on growing your business.
**Tips for Choosing After-Sales Service:**
- **Evaluate Response Times:** Before purchasing, inquire about the average response times for service requests. Quick responses can significantly reduce machine downtime.
- **Check Training Options:** A robust after-sales service should include training for your staff. Proper training ensures that your team can operate the filling machine efficiently and handle minor issues independently.
- **Look for Parts Availability:** Ensure the manufacturer has a streamlined process for supplying spare parts. Accessibility to parts can prevent extended downtime and keep your production schedule on track.
Choosing a filling machine with excellent after-sales service can make a substantial difference in your operational success. Consider these factors carefully to ensure your investment pays off in the long run.
After-Sales Service Benefits for Filling Machines
Evaluating Maintenance Costs: What to Expect for Your Business
When choosing a filling machine for your business, it’s crucial to evaluate the maintenance costs involved. A machine that seems economical upfront may lead to significantly higher expenses over time due to frequent repairs or components that need regular replacement. Understanding the expected maintenance costs is vital for budgeting and ensuring operational efficiency.
Tips: Always research the manufacturer's reputation for reliability and support. Reach out to other businesses using similar machines to gather insights about their maintenance experiences. This can help you avoid costly surprises in the future.
Additionally, consider the availability of spare parts and technical support. Equipment that requires unique components can lead to extended downtimes and increased costs. Opt for machines that use widely available parts or come with strong manufacturer support to minimize disruption in production.
Tips: Implement a proactive maintenance program to help predict and prevent potential issues before they escalate. Regularly scheduled maintenance checks can extend the lifespan of the machine while keeping repair costs manageable and ensuring your production line operates smoothly.
Top 5 Tips for Selecting a Filling Machine with Reliable Support
When selecting a filling machine for your business, support and reliability are paramount. Here are some vital tips to ensure you make the best choice. Firstly, research the manufacturer's reputation. Look for reviews and testimonials to gauge their customer service performance. A manufacturer known for excellent support can save you time and money in the long run.
Secondly, consider the warranty and support options available. A good warranty gives you peace of mind about your purchase, while robust support options, such as on-site service or comprehensive troubleshooting guides, can help resolve issues quickly. Training and installation assistance are additional factors to weigh, as they can significantly impact the machine's setup and operation efficiency.
Finally, verify the availability of spare parts. Reliable suppliers should offer readily available components to minimize downtime. Continuous support also includes software updates and upgrades, ensuring your machine operates at peak performance. By focusing on these aspects, you can select a filling machine that not only meets your needs but is backed by dependable support.
Ultimate Guide to Choosing the Best Filling Machine for Your Business - Top 5 Tips for Selecting a Filling Machine with Reliable Support
Tip Number | Tip Description | Considerations | Expected Outcome |
---|---|---|---|
1 | Assess Your Product’s Characteristics | Viscosity, particle size, temperature | Ensure compatibility with filling machine |
2 | Determine Filling Speed Requirements | Production volume, operational hours | Optimize efficiency and throughput |
3 | Evaluate Automation Level | Manual vs. automatic machines | Reduce labor costs, increase automation |
4 | Understand Maintenance and Support | Service agreements, availability of parts | Minimize downtime, ensure longevity |
5 | Consider Future Expansion | Scalability, adaptability of machine | Prepare for growth, avoid obsolescence |
How Digital Innovations Enhance Service and Maintenance Efficiency
In today’s fast-paced manufacturing environment, the integration of digital innovations into filling machines has significantly enhanced service and maintenance efficiency. Smart technologies, such as predictive maintenance and IoT connectivity, allow businesses to monitor the performance of their filling equipment in real-time. By analyzing data from machine sensors, operators can identify potential issues before they escalate into costly breakdowns, reducing downtime and maintaining production flow.
Furthermore, digital platforms streamline maintenance processes by providing access to comprehensive machine diagnostics and historical performance data. This accessibility empowers technicians to troubleshoot problems swiftly and accurately, ensuring that the right parts are available when needed. Additionally, remote monitoring capabilities enable service teams to assist on-site personnel without the need for extensive travel, further optimizing resource allocation and response times. Through these advancements, businesses can enhance their operational efficiency and maintain a competitive edge in the market.
Comparing Long-Term Value: Filling Machines with Low Repair Costs
When selecting a filling machine for your business, long-term value is crucial, especially when it comes to repair costs. A recent industry report by Market Research Future indicates that companies spend approximately 20% of their annual maintenance budgets on equipment repairs. Investing in a filling machine with lower repair costs can significantly reduce overall operational expenses, making it a smart choice for businesses looking to optimize their profitability.
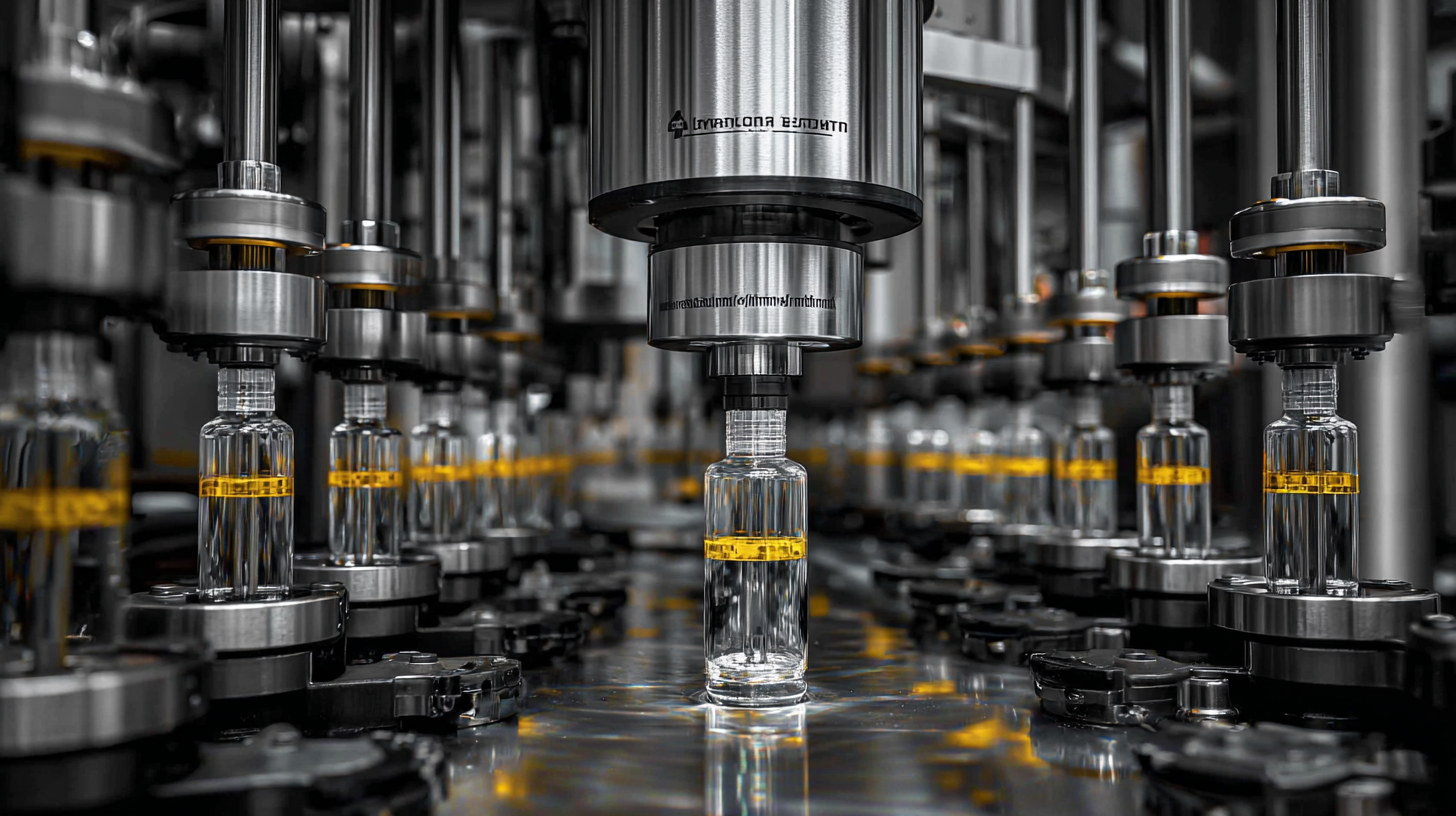
For instance, machines equipped with advanced technology and fewer moving parts often yield lower repair rates. According to a study by the Packaging Machinery Manufacturers Institute (PMMI), businesses that invest in high-quality filling machines experience a 35% reduction in unplanned downtime related to repairs. In contrast, lower-quality machines may initially seem cost-effective but can incur substantial long-term expenses due to frequent breakdowns and maintenance needs.
Businesses should take these factors into consideration to ensure they are not only purchasing a machine that meets their current needs but also one that will provide value over its lifespan.